Contact us |
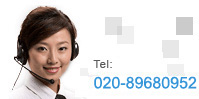 |
ADD:NO.20 Yayao Middle Road Yayao Town Huadu District Guandzhou City
Phone:+86-13728008836
Tel:020-89680952
Fax:020-89680951
Mail: taisheng@gdtsindustry.com
|
|
|
|
|
Home > Industry news |
|
Corrugated cardboard printing machine the main
post time: 2013-5-8 | hits: 5575 |
Water-based flexo printing machine is corrugated cardboard printing machine the main, with the carton packaging sales function is outstanding, the appearance of the carton printing quality requirements become more and more strict, and the factors related to the printing quality is the most important water ink, ink, printing plate system. Ink is like the blood in the body, the blood circulation system in ink circulation system as the human body, is shouldering the important mission. Therefore understanding the ink circulation system for carton printing, ink system to solve the problem of cleaning, maintenance is very important.
According to the current cycle mode classification, water based ink system water flexo printing machine is generally divided into two forms: circulating water based ink system and non water based ink system. The following are the ink system in the form of two and their respective advantages and disadvantages. Water based ink circulation system for ink water circulating water ink system is in the ink supply system in cycles, as shown in Figure 1 Structure ink circulation system, system mainly includes: roller, rubber roller, ink, ink pump barrel, ink tank, ink tank, pipeline etc..
According to the ink transfer mode can be divided into: rubber roller / roller type inking system; positive scraper type inking system; reverse scraper type inking system; closed inking system; combination of inking system. Rubber roller / roller type inking system the inking system consists of a rubber roller and the roller, the ink tank. Rubber roller is in steel roller surface covered with a layer of natural or synthetic rubber produced, generally have high and suitable hardness. Rubber roller, the ink to the roller, and the excess ink from the roller surface scrape.
We
Rubber roller and the roller in contact within the scope of the ink scrape roller network points on, which requires the general should have the following conditions:
L rubber roller and roller speed difference in order to get good scraping effect, direction of the surface in contact line velocity at the rubber roller and the roller and has a certain speed difference, namely, V1 < V2, two roller sliding friction within reach, the roller network points of the ink scrape, therefore, rotating rollers through the gear transmission by a printing plate cylinder and roller drive, can also be driven by motor. Between the roller and the roller speed ratio is not uniform, in general, with the improvement of printing speed, two roller speed difference should be increased.
L ink pressure roller and roller speed once determined, can adjust the contact pressure between the two rollers, the general said the pressure of ink pressure. Here you should pay attention to two points, one is the amount of ink pressure if necessary without it is impossible to achieve good scraping effect; the two is the amount of ink and ink pressure is inversely proportional to the amount of pressure, Jimo larger (two roller center distance A is small), the amount of ink is smaller. Therefore, in the carton printing machine are arranged in the gap adjustment control.
The viscosity of the aqueous ink l ink viscosity is an important performance index of flexo printing ink, it directly influences the stability, transfer characteristics and the amount of ink inking system for the ink, the ink viscosity should be controlled in a reasonable range. Factors affecting the viscosity of ink mainly includes two aspects, namely temperature and diluent content. With the increase of temperature, the viscosity of the ink will be reduced, especially when the temperature was below 15 ℃, the influence of temperature on the viscosity of the ink is more obvious. Therefore, the ink printing environment temperature and temperature control in 20 ℃, stability to keep the ink viscosity and good ink performance will have a significant effect. The viscosity of ink in addition amount of diluent on the ink has a great influence. With the increase of the diluent, ink viscosity decreased, here special attention should be paid to control the content of diluent. If the diluent content too much, although can reduce the viscosity of the ink, but will also reduce the printing density, so that the ink faded, seriously affect printing quality. Practice has proved, better stability properly adding a certain amount of ink in the diluent to keep ink viscosity, diluent content generally 4% ~ 5%. In general, more advanced machines are equipped with the ink viscosity detection device to control the printing quality.
Between L two inclined rollers roll force and roller with a certain pressure, so that the roll deformation, deformation and deformation of rollers is obviously higher than that in the two ends of the central part, the middle part of printing ink amount, and the amount of ink is both ends to reduce, consistency which affect printing ink layer thickness. So the quality of the printing of the impact, and is the biggest bottleneck in improving speed. The actual running at a higher speed in the machine, we can observe the middle part of the ink roller beating, splash, this is between the two roll force caused by extrusion, control on the ink has the certain difficulty. The inking system has simple structure, low cost, low requirement on the roller, poor stability but the amount of ink.
Practice shows that, when the printing speed is low, the printing speed has little effect on the change of the amount of ink, but when printing speed is higher, the change of printing speed will have a greater impact on the amount of ink, the printing speed, ink volume will increase substantially, the printing speed is limited, therefore, transmission this type of ink system is mainly used for low-speed printing machine printing quality requirements is not high. Scraper arranged at the top of the roller inking system of positive scraper, scraper top towards the direction of rotation of the roller.
In the printing process, ink roller network wall scraper back to the fountain, the blade angle can be adjusted according to the need, in general should be 34&#176 alpha. When the ink viscosity, ink mixed with a foreign body, between the roller blade and the surface will accumulate some ink, will produce an outward force on the scraper blade, the blade from the roller surface, affecting the stability of ink amount. In addition, the ink mixed with impurities such as will accumulate, pile plug inside the blade, blade vibration caused by. Compared with the roller / roller type inking system, the improvement of printing speed while also have some impact on the amount of ink, but its impact is not very significant, especially the flexo printing machine for medium speed the ink performance is improved obviously, therefore, the positive blade type inking system currently applied widely, especially the printing on the printing of high quality non halftone, the inking system better. Scraper arranged on the roller or the lower left side on the right side of the inking system of reverse scraper, scraper top back to the roller rotary direction.
Due to blade top back to the direction of rotation roller, the ink is scraped along the roller surface can be back to the fountain, do not accumulate in between, scraper and the inner side of the roller surface therefore, scraper working conditions have been improved, with good scraping effect. At the same time, the blade angle β should also be adjusted. The advantage of reverse scraper type inking system is that how to change the printing speed, ink volume remained stable, the inking performance is the best
Therefore, the network should be printed by reverse scraper type inking system. In addition, reverse scraper type inking system, because of the blade at the top of the stress conditions than positive scraper type, will accelerate the wear and tear on the blade and roller.
Therefore, mainly used for high quality halftone printing ink system of reverse scraper type, laser engraved ceramic anilox roller must use high abrasion resistance. The above three inking pattern generally adopts an open type design. Because of the printing environment, changes in temperature, humidity and mixed with various impurities, the performance of the ink is very difficult to maintain stable, will not only directly affect printing quality, but also cause the scraper blade and roller surface scratch.
Therefore, modern flexo printing machine generally adopts a closed type inking system. Scraper type closed cycle system closed inking system closed roller, inking system is scraping knife, ink, the ink reservoir and inking pipeline and other components are arranged in a closed container, in order to ensure that the ink is not influenced by the external environment, its basic structure as shown in figure 5. Enclosed type inking system generally adopts the reverse scraper, reverse blade not only can move left and right, adjusting device and a clutch device and is also provided with the blade angle, when the shutdown, scraper should be promptly leave roller. The roller is laser engraved ceramic anilox roll, in addition to a pressure adjusting device, when stop roller by auxiliary motors can also maintain the uniform rotation, in order to prevent the ink roller surface curing. In addition, in order to improve the cleaning effect, should be fast docking can realize the inking system and automatic cleaning system.
Enclosed is mainly used for high speed printing machine evenness of narrow and wide format ink system type, may take the following measures:
1) the ink roller processing into the drum, to increase the amount of ink on the scraping roller central parts of the.
2) inclined installation method. The roller bearing with tilted installation method.
3) install the ink roller, bearing the operation side of the downward adjustment, adjustment of the bearing in the transmission side of the center of rotation, the rubber roller and the roller cross an angle alpha,
4, the results will increase the central part of the roller scraping, and both ends of the scraping amount is reduced, the error to compensate for the roll deformation caused by.
5 important parts, ink circulation system: ink pump generally using pneumatic diaphragm pump, the application is more one-way pneumatic diaphragm pump. The basic structure consists of a working chamber and pneumatic cavity is composed of two parts, the middle diaphragm separated.
The compressed air from the inlet into the air cavity, the pressure increases the diaphragm to move left, the spring is compressed, one-way valve is opened, the medium pressure in the working chamber, pneumatic left valve closed air inlet, air valve, pneumatic sleeve, the pressure chamber, an inlet air discharge, pneumatic cavity decompression the diaphragm, reset and push right, the inlet opening, into the next action cycle. Continuous reciprocating motion guide medium suction and discharge, complete the delivery medium.
Now import the flexible carton printing machine in the use of bidirectional pneumatic diaphragm pump as power ink circulation, its characteristic is: the ink not by natural gravity flow back, and the ink is sucked back into the. In addition, high-grade ink flexo printing machine, in order to maintain the stability of the ink by peristaltic high-speed rotary pump, can prevent the ink bubbles, and a strong magnet is installed in the ink inlet, absorb the impurities in the ink.
Many kinds of scraping knife, thick see is a thin steel sheet, but it is the most common knowledge is of two kinds, namely: ordinary type stainless steel scraping knife and polyester plastic scraping knife. Ordinary stainless steel blade is divided into: general steel scraping knife and high-speed spring steel scraping knife. General steel scraping knife is also called economic type scraping knife. Some kind of blade steel only after processing in general, so hard and not issue research since the knife edge, its characteristic is cheap, long service life (for reasons of steel hard).
However, because of the high hardness, so wear coefficient on the printing plate roller is also increased. In addition, since there is no cutting edge, in order to ensure the contact angle plate good and the ink scrape excess plate surface, we must exert a lot of pressure on it, along with the increase of working time, mutual friction between scraper and roll them, cross section contact part of the product will continue to increase, thus the scraping, very adverse, will cause the printing image tone change. There knife line, roll chromium layer wear etc.. In this case, in order to ensure the quality of printing, printing must continually stopping, turning, grinding the blade replacement, adjustment, which will delay time. And reboot this process will result in the waste of raw materials, every single time.
High speed type spring steel scraping knife mostly through the processes of production and processing to strict manufacturing, the scraping knife is mostly imported products (recently technology of domestic production is not pass), the scraping knife is provided with a self grinding edge, so before use without turning knife mouth can ensure good contact with the plate. To achieve the best ink scraping effect, so that the ink scraping clean, transfer the amount of ink is more uniform, more consistent. If the operating properly, such as contact angle is adjusted to the proper, uniform pressure, it can greatly reduce and even eliminate the printing process "cut" or "fog".
Although the doctor will continue to wear, in the printing process but, contact area in the entire length of the scraper directions are always remain unchanged (unless the edge grinding end), therefore, need not worry about the printing product pattern image halftoning occur not consistent image, because of its special steel and the production process in the whole smelting on the essence of refining forging processing and polishing the most suitable for scraping with the cutting edge, so to ensure scraping the chromium layer and grinding effect and not to hurt the roll surface of the best. Although the scraping knife, prices are more expensive than ordinary type scraper, the price but, printing manufacturers are happy to use, because when using the squeegee print, because it can reduce machine grinding blade and over time, while reducing the stopped, the boot process adjustment and control of laminated color process printing substrate waste, so that the reject rate is greatly reduced, so the relative also reduces the production cost, and thus directly or indirectly increase the economic effect.
Plastic scraping knife is made of polyester, high molecular weight polyethylene plastic, with good toughness is more fitting roller scraping effect, has good low squeegee pressure, squeegee roller service life extension and without solvent erosion, without any metal particle mesh plug installation is simple, use more safe for anilox roll and metal roller in the majority of high-grade corrugated cardboard printing machine adopts scraper type closed cycle system has its own characteristics: ink into the ink hose to the ink to blade groove, upper and lower blade and roller is within the 30-35 degree angle, scraping knife scratch gently release ink roller, making ink film thickness uniformity. Then the roller ink transferred to the printing plate, corrugated cardboard paper down, through the printing plate drum and nano imprint lithography drum, adjust the gap between the printing plate drum and nano imprint lithography drum, the plate of information transfer to corrugated, complete the printing process. The gap to control the nano imprint lithography drum and a printing plate cylinder in the debugging process, the plates of the rollers and roller gap, the gap between the rolls on the traction. When working, the air compressor with compressed gas to pneumatic diaphragm pump pulse and the ink storage tank by suction inking pipe pump to the printing ink to printing ink tank.
The ink tank wall is provided with an upper limit of quantification of ink backflow hole, then the ink conveying tube is connected to the ink storage tank. When the ink in the ink tank more than quantitative backflow hole, ink through the reflux hole through the ink conveying tube automatically flows back into the storage tank, and then by the ink pump to the ink tank, so go round and begin again to carry out, so that the ink to form a circulation flow. Ink supply amount can be achieved by adjusting the pump intake amount of ink or ink supply valve, in order to achieve ink. Compared with the closed-end scraping knife and two roller type, positive scraper, reverse scraper structure, advantages of closed-end scraping knife is the biggest good sealing, using reverse scraper structure quantitative ink supply system, suitable for high-speed operation, reducing the solvent ink volatilization and metamorphism, solving the water ink bubbles often appear. At the same time, the system can automatic cleaning, reduce the ink change time and stop time. Sealed by the ink chamber type reverse double scraper device (also called a scraper seat), two scraper, ink type two section with side making wearable soft material seal plate and the roller to form a closed chamber.
The ink chamber is provided with an ink outlet and an ink outlet, an ink inlet of the pump by flexo ink onto the roller surface and stored in the ink chamber, inking after scraper scraping, scraping the ink can be recycled, greatly improves the utilization rate of the ink. Cavity knife system two scraper effect each are not identical, a reverse type, a reverse blade, used to scrape off the excess ink roller; another is positive, positive sealing blade, play the role of sealing. Enclosed type scraper system is a tool to improve the printing quality, also will be widely applied in china. Automatic ink circulation system can effectively improve the degree of automation of the printing operation, reduce the ink consumption, reduces the operation difficulty, to improve the printing quality. Especially for improving the printing ink uniformity and transfer performance, ensure that the ink in the printing process relative viscosity, concentration, stability and improve the printability of ink and color effect has the effect and the role of the.
The new ink circulation, cleaning system is a kind of automatic ink delivery, cleaning system, which is characterized by flushing computer control ink pump speed, direction and system. The pump is operated by a motor, the whole system can be composed of a central PLC to run or printing machine is connected directly with the output. Printing is completed, the ink in the ink to ink suction bucket, then, began to water rinse cycle for automatic flushing. After washing, the fountain in the wash water is sucked back into the. Conveying the ink and wash can be automatically controlled by a computer, convenient operation, time saving, labor.
Non circulating water based ink system non circulating water ink system make both ends of roller and roller baffle closed, the roll groove of the ink and placed in the ink box of ink roller at the top of the cycle, in order to ensure the stability of viscosity. Both ends of ink system in ink roller and rubber roller is equipped with the ink tank. At the top of the inking device mounted on the printed parts, and is equipped with a two ink pump, has a fixed small ink box between them. Ink supply device along the roll axis to move back and forth continuously supplying ink, and the recovery of residual ink, quickly returned to the circulatory system reuse. As shown in figure 7.
The device has three advantages: reduced L for a single ink loss to reduce ink loss for a single, larger contribution to reduce the production cost. Consumption of printing ink ink printing each rollers form for single generated is about 700g, closed type scraper is about 200g, and the scraper Japanese plum Valley is 50g. According to the daily in 30, annual production of 360 day, have a great difference. Also, cleaning equipment needed to water is also great, not only a waste of money, bring the negative influence to the environment.
L short for a single time past circulation type ink printing color changing time 5 ~ 20 minutes. This is because the recovery principle is through the natural flow of ink and ink recycling, pipeline to long for cleaning, this structure even with mandatory recycling system of ink, only can save about 1 minutes.
Non cyclic ink supply system, mandatory recycling device using special ink, change can be completed in 3 minutes. Compared with the circular ink printing, this way to save a lot of valuable work time, thus effectively improving the production efficiency, reduce production cost. Due to the use of non cyclic ink system closed, thus reducing the ink loss, in the replacement of color group at the same time, also can automatically clean the wastewater.
L in order to reduce ink consumption, and shorten the cleaning period, when a job is completed, the two pump began to quickly absorb between two large ink roller. Once the ink recovery is completed, an approximately 7 ounces of a small amount of water will be from the upper end of the pipe ink device in flow from the cleaning roller, and a scraper is arranged at the bottom of the rubber roller shaft and residual ink were blown away with the pipeline, printing parts on the edge of the inflow of wastewater collection tank. In addition, in order to better for the maintenance of the system, the printing operation after the end, change the ink color, should clean the ink system. Generally has three buttons on the control panel of machine: ink pump switch button, switch button, the rollers rotate button cleaning. In order to clean the ink rollers, ink roller in the rotary state shall ensure that.
Now more advanced printing machine, ink cleaning system is entirely by computer software system settings, figure 8 is the control interface. Carton printing machine ink circulation system is an important system speed, printing quality, printing machine is the continuous technology progress of the site, so we in the purchase, use should combine their own requirements to match the ink system mode.
|
|
|